A most unlikely combination of pure science and a touch of that special something that makes the music come alive.
The
LAMM
Way
The Standard Bearer
A synthesis of pure science and finely honed musical instrumentation. A reproduction process that releases the listening experience from the constraints of electronic equipment. Far beyond a studied combination of circuitries, metal boxes, and trial-and-error prototypes.
These elements are what has set Lamm Industries’ designs apart since its founding in 1993. Today, nearly three decades later, the family-led enterprise of sonic excellence continues—with a legacy of award-winning equipment heralded as the reference standard for audiophiles around the world— from our LL2.1 linestage preamplifier to the ML3 Signature monoblock amplifier.
Our Origins
LAMM Industries was the brainchild of visionary Vladimir Lamm (1945–2022).
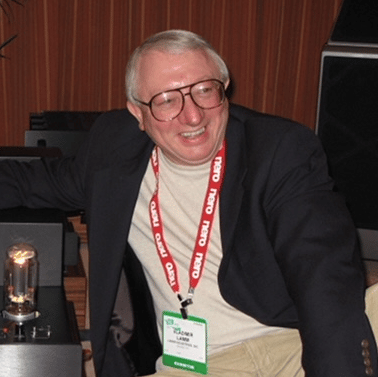
In Memoriam to Our Founder
Vladimir Lamm
1945-2022
May his memory always be for a blessing
Similar to the heightened build of a musical crescendo, LAMM Industries represents a determined pursuit of experience, innovation, and excellence—towards which Vladimir Lamm dedicated a lifetime.
Vladimir Lamm’s extensive experience in the field of sound reproduction and psychoacoustics, the scientific study of sound perception and audiology, led to his developing the theory of a “human hearing mechanism.” This theory served as the basis of his designs and sound reproduction techniques. By experimenting with an array of electronic models related to the theory, Lamm landed upon a limited set of topologies that enabled him to create sound reproduction equipment with predefined and predictable parameters—establishing the crucial need for listening tests as an integral process of product development while simultaneously eliminating the use of a trial-and-error approach to design.
Since the physical prototypes of new models are based solely on calculations, the design is essentially ready for production once the prototype is finished. The result of this extensive work is a number of hybrid and vacuum-tube designs, each setting a benchmark of excellence in its respective category.
Exceptional Quality
At LAMM Industries, we believe that what is not seen is as important as what is seen.
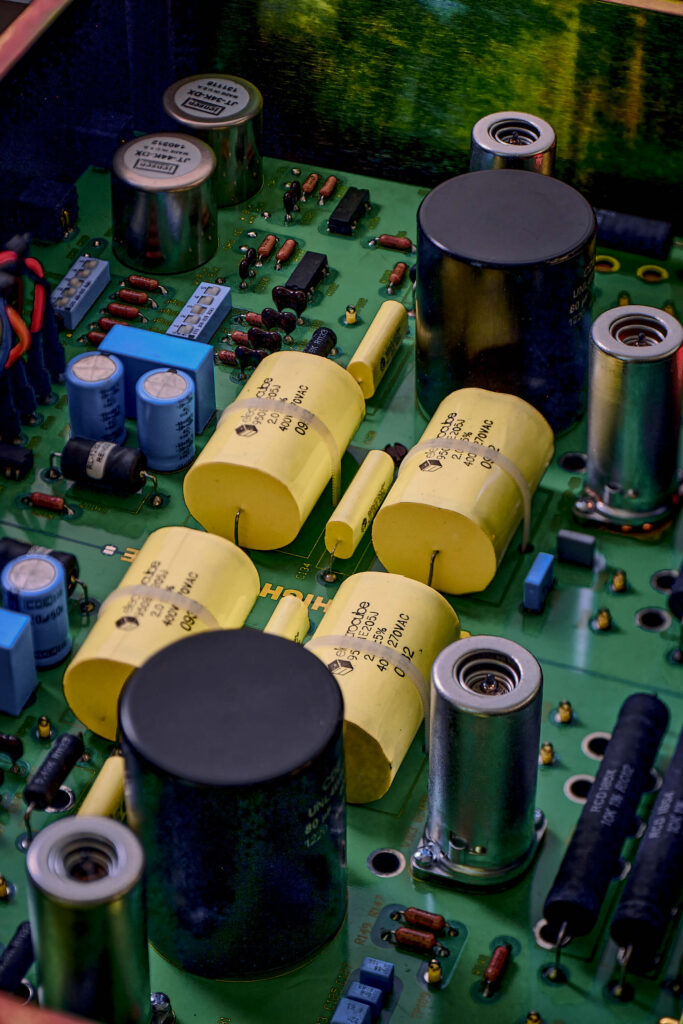
That is, details matter. At every stage.
To that end, strict quality control is maintained throughout the production process. Every module and assembled printed circuit board (PCB) is bench-tested, followed by an eight- to ten-hour burn-in period. The product is then assembled and tested, followed by a 72-hour burn-in period. The burned-in units are then retested and remeasured. The “pre-burn-in” and “post-burn-in” measurement results are recorded in a production report, which is routinely maintained for every piece of equipment.
Design Details
LAMM Industries products operate on universal AC voltages and do not require elaborate modification. Products are shipped with great care in custom-made, heavy-duty wooden crates.
All LAMM products are made with top-quality materials (including military-grade), high-end components, and custom-designed transformers, utilizing the most technologically advanced processes available. Equipment interiors reflect their handcrafted design and a well-considered balance of component arrangements. The external design is elegant but not showy, underscoring our philosophy that state-of-the-art audio equipment exists to amplify the listening experience, not serve as a showpiece.
The LAMM customer seeks a truly refined musical immersion and will settle for nothing less than a superior sonic experience.
Vladimir's Thoughts
LAMM equipment represents a life-time investment. It actually saves one a lot of money in the long run by eliminating the need to constantly upgrade one's system.
The conventional wisdom, in the mass-market world, is that all amplifiers sound pretty much the same, as long as they have the same number of watts and the same levels of “total harmonic distortion'' (THD). But I realized very early on that this just wasn't true. For example, you can look at the ratings for a Japanese amp (with THD of 0.0001 %), but when you listen to it, the sound is just terrible. It was hard for me to accept this, as an engineer, but I came to a conclusion that the conventional measurements have nothing to do with what we hear.
My ultimate aim, like that of many in the high end, is to build equipment that has no sound at all, that brings the listener as close as possible to the musicians and singers in the studio (or at least to what they laid down on the tape) with minimal interference from all the electronics in between.
I am a scientist, not only an engineer. I developed electro-mechanical models which describe the hearing mechanism of the human ear. I use these models when I design equipment. I never do listening tests because I already know how the equipment will sound.
Each amplifier that I design is a model that represents not only our ears but also our hearing mechanism. This is the foundation, based on topology, for every amplifier that I make. It is not something I got from books or anywhere else. Now, when a component is near or far from that reference topology (in addition to some other factors), I can immediately tell how that amplifier will sound. Also every topology has its limitations with the exception of single-ended. Single-ended has no limitations, only price points.
In general, all pre-amplifiers that use solid state technology don’t sound right. It’s something connected to the actual topology. When I design my equipment, naturally I employ some standard topologies as building blocks, but what is important is how they are used and in what combinations.
See, the thing is, we are created a certain way. One can argue that our ears or your nose are not optimally designed, that they could be better, but that is how we are created. One can’t dispute that. One can’t change nature. The same argument holds with output transformers. You can love it or hate it but it would be the same to say that you don’t like the way your hand looks. But that’s the hand you have and you can’t change that. Again, it’s the same with the transformer. It does something – so, it’s an absolute must. Why do you think I put a capacitor into my topology between the input and output stages? In order to improve the quality of bass, to make it natural. Remember that today we have industrial standards, something like standard topologies used by the industry. Direct-coupled amplifiers without capacitors are destroyers of good sound. And even if the majority of designers develop them - so what! The majority is not always right. The majority can be aggressive about their beliefs but that does not mean they are right. And that’s that. It almost sounds too simplistic for the majority of engineers – in order to improve the quality of bass you have to use a coupling capacitor.
What I do is not black magic. I don’t belong to that group of audio designers that create designs through experimentation and tweaks, or listening tests for that matter. I am an engineer. I use the laws of physics and I know what I am doing. Of course, even if my amplifiers satisfy my requirements and are properly designed, if I used inferior parts, or inferior power supplies, there is no sound. They wouldn’t sound as good as they could.
The majority of my research on the human hearing mechanism was conducted while I was the chief designer at the audio company, but it was done privately. My engineers had no idea what they were involved in. It was a huge undertaking; it was the Soviet system after all, a lot of equipment, a lot of people. I was in charge of about 400 employees. Now this might sound so easy but, in reality, I went through hell. I had no idea how to get started but I did understand that there was something seriously wrong with the current audio design (at that time). I did hundreds of experiments; and I did listening tests of different topologies. And then, after analyzing the results, I started to see the light at the end of the tunnel. And that is was formed the foundation for my theories (it was around 1976).
When I worked for the military in the early 1970s, we did a lot of groundbreaking research. I am referring to high definition television, HDTV. And it was done before the Japanese; we started in 1971. A part of my job, a very important part of my job, was designing high frequency video amplifiers, 20 MHz, 60 MHz etc. I couldn’t use traditional methods for designing video amplifiers because of the high frequency response requirement. So I developed alternate methods. How does one design such an amplifier? It was almost intuitive, my intuition. I then applied some of these techniques to audio design and got interesting results. These methods were so different than the standard used by audio engineers that it started me thinking. And then I started my first experiments.
All Lamm designs are rooted in methodologies that I developed based on my ALS theory (Absolute Linearity of the System). In general, these methodologies, along with some additional conditions, define the type of topologies that I find necessary for implementation of a specific product in a specific price range. Having said that, I need to point out that my criteria for choosing the methods of implementation lie outside of the mainstream (typical) solutions. And, as a result, the terminology that I would use for describing those methods would sound unfamiliar to most.
Everything is important. Each part of an audio system must be properly designed because even a small less important part of the system can destroy the entire presentation.
This solid-state amp (which, by the way, is capable of continuously delivering 770W of brutal power into 1-Ohm load) can double up as a welding machine! [the demonstrations showed that the M1.1 really emitted sparks like a welding machine].
Generally speaking, a natural approach to reproduction of sound is using horn designs. They, however, have to be properly designed. Another natural approach involves using infinite baffle designs but for that you really need a large room, practically a castle. At some point I had access to Siemens Eurodyne speakers. The sub-woofer, the mid-range and the horn tweeter were imbedded into a piece of metal. That is attached to a wooden board (4 x 4 m) – infinite baffle principle – and you are in heaven.
If we are talking about the audio equipment that should truly belong to hi-end category, it must be designed as close as possible to the real human hearing needs. Designing the equipment of such level is, indeed, a lofty and complicated task. I just must add that it is quite difficult to maintain the balance between laying claims to designing the real state-of-the-art equipment and not sacrificing the academic design approach to the marketing hype. It is difficult from the viewpoint of ensuring commercial success of such equipment.
On the one hand, the designer operates with the sword of Damocles over his head, which is the cost of building. On the other hand, there is a desire to create the most perfect product, which unavoidably leads to increases (sometimes, quite significant one) in the cost of building. The next step is to resolve purely technical tasks related to reliability and longevity of the product, its maintainability, etc. which, in turn, demand the utilization of very reliable components expected to perform flawlessly over long periods of time.
My total accumulated knowledge had led me to an understanding that there exist a very limited number of topologies suitable for creating truly high quality audio equipment. In my opinion, utilization of these methods sets very high standards in equipment design and, in turn (as was mentioned earlier), leads to the increase in production costs that determines a correspondingly high retail price. At the same time, we are able to immediately hear the difference between the system based on my design principles and other systems.
Design – in order to develop a product that conforms to my sound quality standards, I spend as much money and resources as necessary. Besides, it is necessary to take into consideration the fact that this product will have to be manufactured in quantity, be technological, not require any future upgrades or modifications, and ensure the level of reliability specified at the development stage.
Component quality – I choose the highest quality components that not only ensure the reliability of our products but also have optimal characteristics from the standpoint of transmitting the sound (in other words, components that have minimal sonic signature).
Aesthetics – It is my firm conviction that the end product in Hi-End audio is the sound itself, whereas all those boxes into which the electronics are packed are a “necessary evil.” Based on this principle, I try to create the equipment that is visually as little noticeable as possible, and that attracts minimal attention of the listener. Speaking more plainly, I prefer the “form follows function” approach that works with the established tradition of designing the “pro-audio” equipment. I also partially utilize the concepts suggested by W. Morris at one point, along with certain principles of W. Gropius (“Bauhaus”).
Quality Control – This issue receives our most serious attention. At the conception of each design, we carefully consider its break-down into functional blocks or units in such a way that would allow us to check each block independently. Simultaneously with the development of a new product we design the test-stand specifically for testing of this product.
gives a fairly good impression of the costs involved in quality control.
I am working with tube, solid-state, and hybrid technologies utilizing single-ended (class A) and push-pull (class A and class AB) topologies. However, my personal preference is with the single-ended topology that employs vacuum triodes in the output stage. The advantage lies in the real possibility of achieving the level of sound reproduction that closely approximates the actual sound of live instruments in space.
[In answer to this question: “Has amplifier design reached its zenith where further improvements are marginal, or will the next decade produce even better-sounding preamplifiers and power amplifiers?”]
For the sake of brevity, I will once again use an allegory. We know the names of great masters -- Amati, Guarneri, Stainer, Stradivari, etc. -- who became universally known and respected for their unparalleled creations of bowed stringed instruments. These instruments have passed the test of time, which is generally a determining factor in evaluating the real worth of any object and/or idea. In this day and age, while possessing very impressive scientific and mathematical knowledge, along with access to powerful technologies, we nonetheless can only approach the previously accomplished mastery level when producing the same type of instruments.
Please note that whether we are talking about the musical instruments or electronic audio equipment, we are dealing with devices that interact with the human structure itself -- in all its complexity. I think that if future research in the field of high-end audio will take this – and all related factors -- into consideration, and begins work in this vein we can expect very interesting and serious results.
If you ask Vladimir about how his…old amplifier design remains viable today, his response is emphatic: “…foundation in how humans perceive sound remains unchanged.”
The elements of “naturalness” and “neutrality” are central to all LAMM products. Our aim is to create equipment maintaining its own neutrality while conveying all kinds of emotions inherent in the music material and its performance -- a sort of a medium that is not involved in the process, yet sensitive enough to perceive and transmit all sorts of musical information and feeling. The notes themselves are not yet music – a gifted performer is needed to bring the notes to life in the most wholesome sense. The lifeless body of a bird, for example, is not exactly a bird – some sort of spark is needed to bring the bones and plumage alive. Likewise, sound reproduction equipment itself does not guarantee the ultimate listening satisfaction; listening is a complex process and touches upon various levels of the human being. I had spent many years developing the methods that will bring some sort of spark to audio components and with them, the possibility to merge with the music.
Through our equipment we strive to make listening to the music a meaningful and deeply satisfying experience.
It is always gratifying for me to know that a person becomes absorbed and moved when listening to music through LAMM electronics. And, although audio components are merely the tools in assisting us to relive the musical events, we all strive to re-live those events to the fullest. …I cannot stress enough the importance of proper matching of the system components within any level. Ultimately, each component should sonically be as neutral as possible within the limitations of each particular topology, in order to assure the maximum neutrality of the system. The idea behind any of my designs was to create a piece of equipment as self-effacing as possible.
One of my goals, while designing the L1, L2 Reference and L2.1 Reference preamps, was to put the issue of “tubes vs. transistors” at rest. Our own experience in this regard, backed by that of our customers and various reviewers, has been summed up aptly by Art Dudley [a prominent audio reviewer who had, sadly, recently passed away]: “During its time in my system, the Lamm L2.1 Reference was the rare product that swept the questions of tubes vs. solid-state into insignificance, focusing my attention on the music…” And that – coupled with what I believe to be an impeccable design -- was exactly my goal.
View Awards By Product
M1.2 Reference Amplifier
M2.2 Amplifier
ML2.2 Amplifier
ML3 Signature Amplifier
LL2.1 Preamplifier
L2.1 Reference Preamplifier
LL1.1 Signature Preamplifier
LP2.1 Phono Preamplifier
LP1 Signature Phono Preamplifier
M1.1 Amplifier
(Discontinued)
M2.1 Amplifier
(Discontinued)
ML1 Amplifier
(Discontinued)
ML1.1 Amplifier
(Discontinued)
ML2 Amplifier
(Discontinued)
ML2.1 Amplifier
(Discontinued)
LL2 Preamplifier
(Discontinued)
L1 Preamplifier
(Discontinued)
L2 Reference Preamplifier
(Discontinued)
LL1 Signature Preamplifier
(Discontinued)
LP2 Phono Preamplifier
(Discontinued)
Best In Show
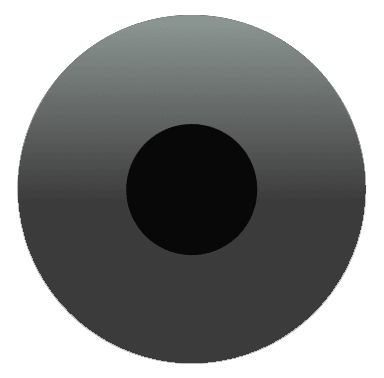
2001
The Best Sound at Home Entertainment 2001 Show
Stereophile
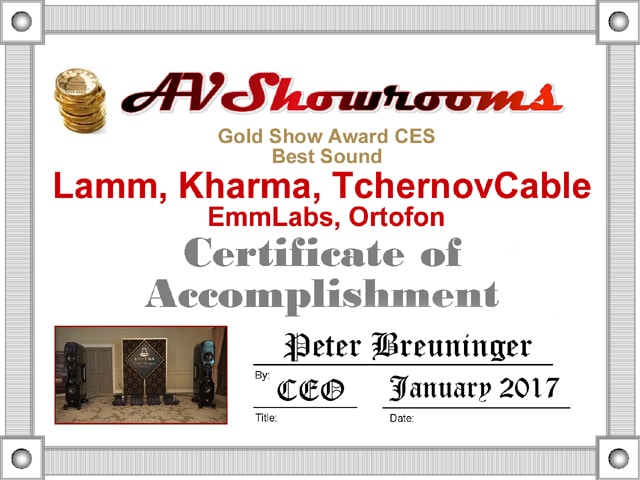
2017
AV Showrooms Gold Show Award CES - Best Sound
AV Showrooms
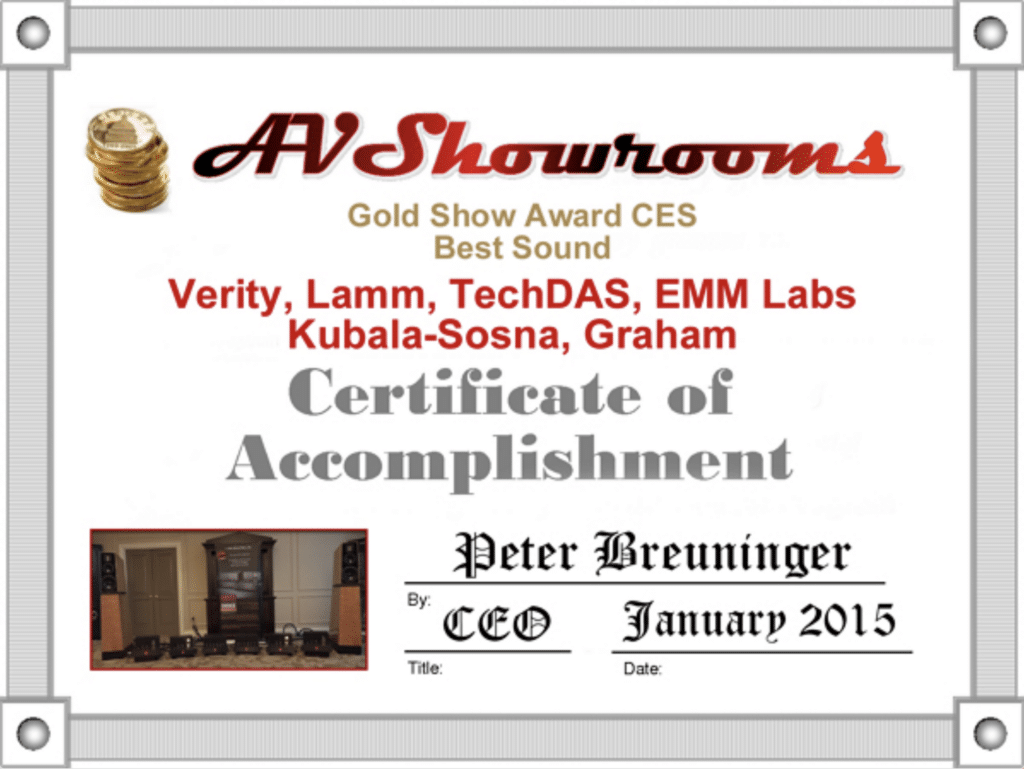
2015
AV Showrooms Gold Show Award CES - Best Sound
AV Showrooms
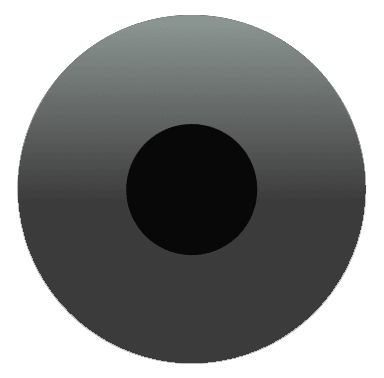
1993
Best Sound at the CES 1993 Show
Audiophile (Hong Kong magazine)
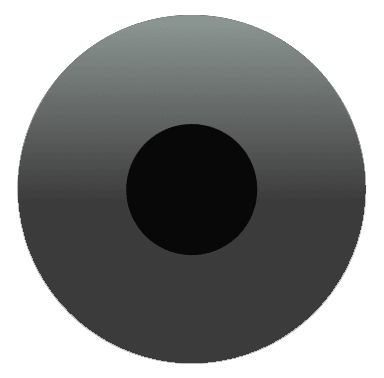
1993
Best Sound at the CES 1993 Show
Stereophile
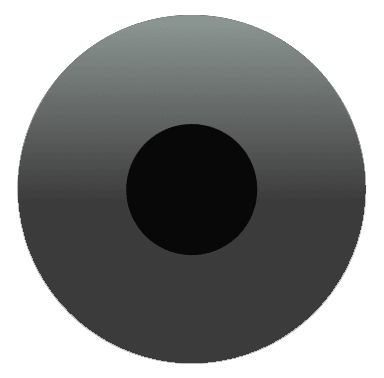
1999
Moscow HI-FI'99 Show "Best Sound" Award
Moscow HI-FI'99 Show
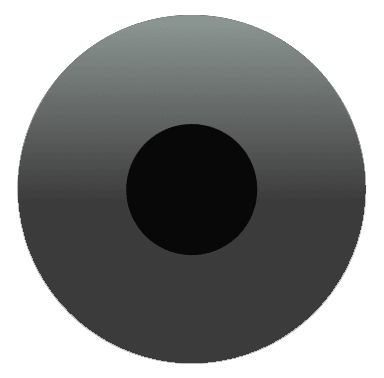
1998
SoundStage! CES 1998 - Standout Room
Soundstage.com | CES 1998
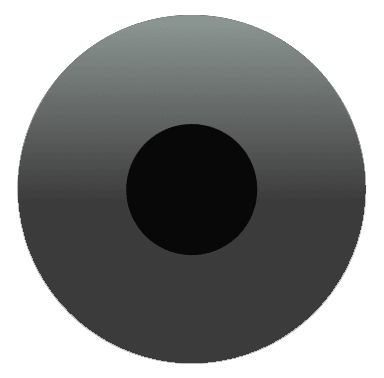
1999
SoundStage! CES 1999 - Standout Room
Soundstage.com | CES 1999
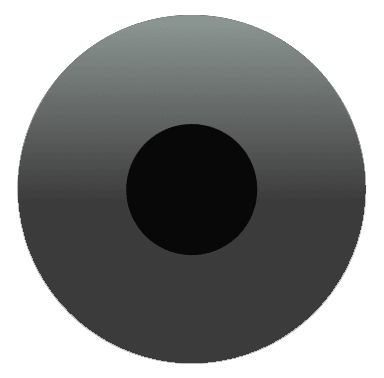
2000
Sounds of CES 2000: [TAS] writers pick their...best exhibits of the Show
The Absolute Sound
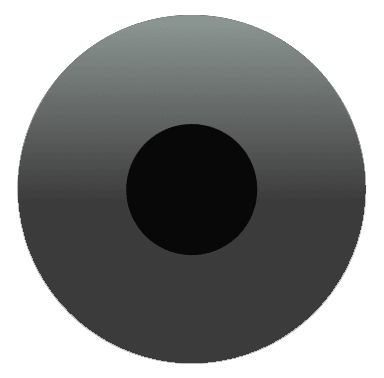
2000
SoundStage! CES 2000 - Standout Room
SoundStage! | CES 2000
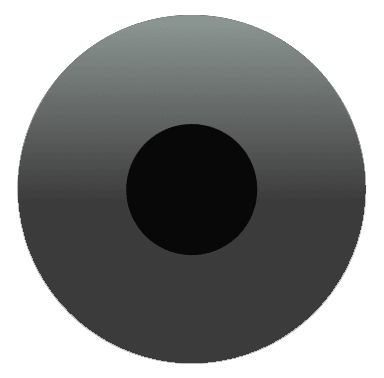
2001
SoundStage! CES 2001 - Standout Room
SoundStage! | CES 2001
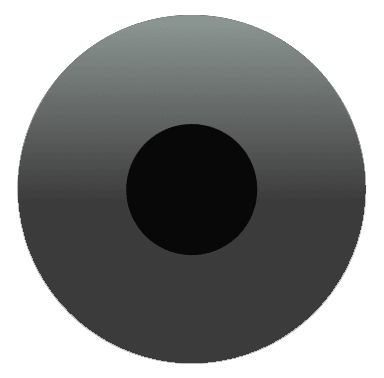